Managing Risk through Quality Control Field Testing
25 Oct 2022
Field testing is fundamental in the building and construction industry to ensure safe and compliant project installations
In the building and construction industry, testing products like windows, walls, and doors in the lab is just the first step to ensuring the quality and safety of the overall project. The next step is testing the actual construction project in the field. We do this for a few reasons. Quality control is one major aspect of field testing, whether it be for a new construction project or for building façade renovations and improvements, to help ensure the safety of the installation.
Lab testing vs. field testing
Lab testing is performed on a prototype specimen to certify or validate product performance ratings. Manufacturers perform lab testing for things like air infiltration, water infiltration, and to determine where products can be sold
Field testing is performed on "newly" installed products to verify the installed performance of the product and the installation. This can be a new window in an existing building or a roof in a new build. In the building and construction industry, it's important to test the product and its installation out in the field as it becomes part of an overall structure.
One type of field testing we conduct is forensic testing. In the building and construction industry forensic testing isn't quite the same as what you see on your favorite serial crime drama, but we do employ scientific methods to identify a "suspect." For example, we use forensic testing to test wall assemblies with known water control problems to accurately identify suspect wall construction components and details. Forensic testing can be performed on any portion of the building envelope, roof, walls, or fenestration products.
We employ field testing for a variety of different projects, including new construction, building façades, renovations and improvements, replacement (e.g., windows), and remedial and maintenance verification. Field testing is also used to support litigation actions.
The best time to perform field testing
It is vitally important to perform field testing as early in the installation process as possible. The chances of running into issues that require rework increase the further into a project, and the rework can become more complicated. This is typically done by an on-site mock-up, which can be an on- or off-structure mock-up, to detect any possible problems prior to completing the project and prior to installation of interior finishes (insulation, drywall, trim, etc.) for which you need visual access to the test area.
It's also important to continue testing throughout the entire installation of the project during different intervals of installation completion: 10%, 35% and 70% are the typical points that are called out in project specifications to ensure testing early in, part-way through, and at the end of a project.
Performance criteria
The information required in order to perform field tests and meet the project requirements is considered performance criteria, which should be discussed with the parties involved prior to scheduling the testing. Some key considerations for performance criteria include:
- What test methods are being performed in the beginning stages (including test pressures)
- Maximum allowable air infiltration rate to determine pass or fail
- Definition of water leakage changes with standards
- On-site requirements (power, water source, access ladder, scaffolding)
Performance criteria can be obtained from a number of sources, including project specifications, industry documents, building consultants, manufacturer/installer, and engineers and design professionals.
Key takeaways
When it comes to field testing, it's important to understand the critical performance characteristics of a building's envelope per the job specifications. You should test all unique façade conditions that are used on the job, in many cases it's the worst-case scenario that you want to test. It's crucial to specify and recommend during field testing to mitigate risk during and after construction to ensure the building performs when complete. And finally, be sure to review project specifications carefully before you start construction.
For more details about the specific types of field testing as well as a closer look at the test methods involved, watch our on-demand webinar – Managing Risk through Quality Control Field Testing.
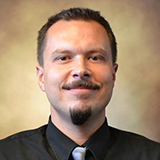
Stephen Shank,
Regional Manager – Lab & Field Services
Steve Shank has more than 20 years of experience in the testing of architectural products. As a regional manager for Intertek's Building & Construction business line, he has current knowledge of field-testing procedures, specifications, and standards for building and construction products and installations. Steve also mentors staff within the Northeast and interacts with clients and establishes safety protocols. He also holds a FenestrationMaster®Professional Certification.