Why Performance Testing is Critical for Modern Medical Devices
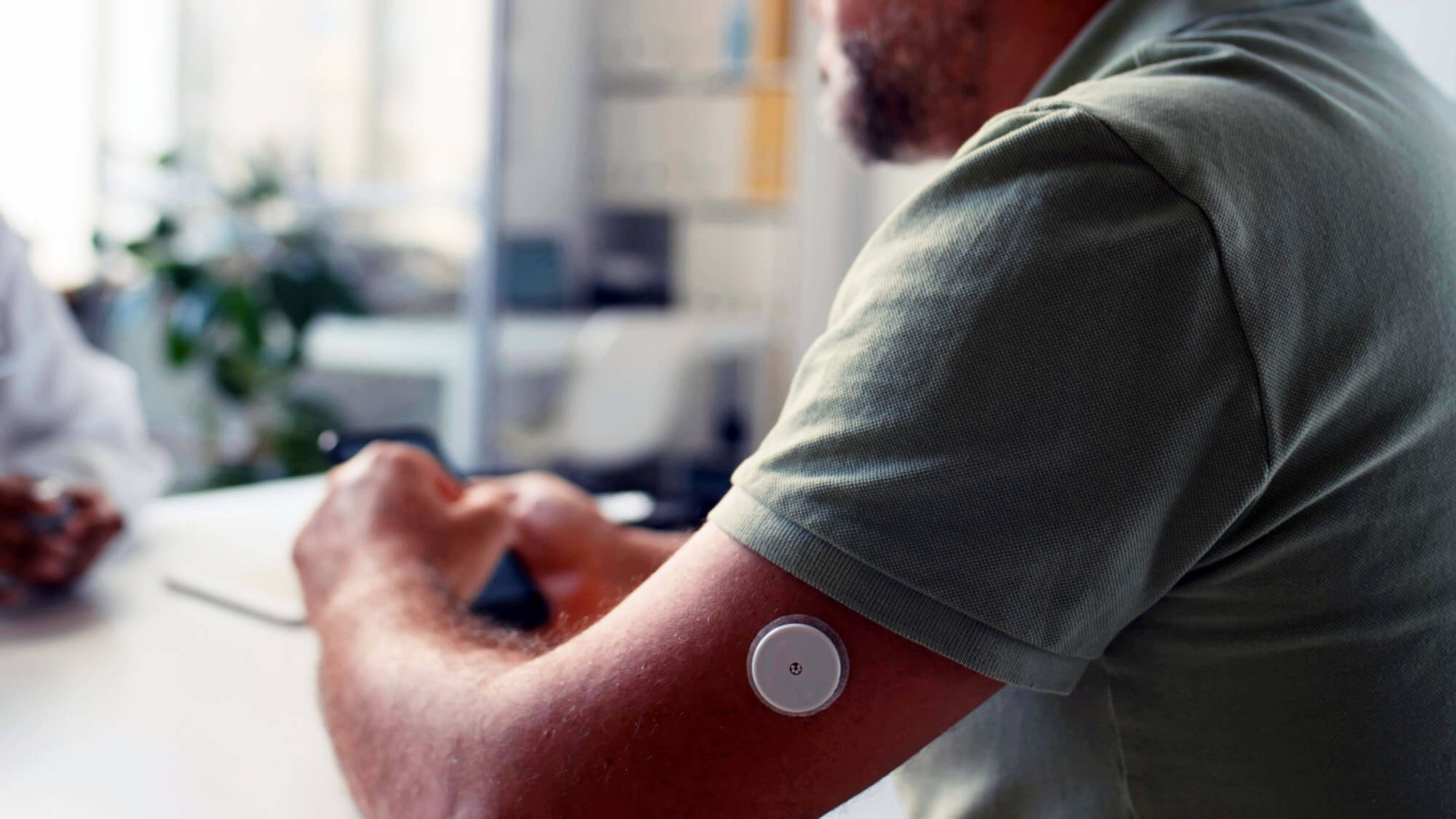
10 Jul 2025
As devices become smaller, smarter, and more mobile, performance testing ensures they deliver when and where it matters most
Medical Devices Have Left the Hospital
Medical devices are no longer confined to sterile, controlled clinical settings. Increasingly, they're being used in homes, offices, schools, and even on the move. The shift toward consumer-facing health technologies, such as wearable monitors, portable diagnostics, and smart therapeutics, has placed these products directly into the hands of patients and caregivers, many of whom have no clinical background. This change has dramatically broadened the conditions under which devices must perform. A glucose monitor may sit on a nightstand in Arizona’s summer heat or get tossed into a bag on a cold winter morning in Minnesota. A digital thermometer might be used by an elderly patient with reduced dexterity, or by a parent trying to calm a squirming child. In all cases, performance cannot be compromised. Devices must work as expected – no matter the setting or the user.
Beyond the Lab: Understanding Performance Testing
Performance testing goes far beyond verifying that a device works under ideal conditions. At its core, it’s about understanding how a product behaves in the real world, under real stress. It asks fundamental questions: Does the device perform its intended function reliably and accurately? Does it tolerate environmental and physical challenges? Will it maintain its integrity over repeated use?
This type of testing often includes simulations of harsh use, including drops, vibration, moisture, or extreme temperatures. But it also considers more subtle challenges, such as whether the product's buttons or interfaces are intuitive enough for users with reduced vision or dexterity. Can it maintain connectivity when a patient moves between rooms? Will it deliver consistent readings despite small environmental fluctuations?
The answers to these questions often emerge not from formal verification testing, but from thoughtfully designed performance evaluations tailored to the product’s actual use scenarios.
Testing Early, Testing Often
In many organizations, performance testing is mistakenly reserved for the final stages of development. But some of the most valuable insights emerge when testing begins early – during concept design or even vendor selection. Early testing can reveal whether a new material will hold up to sterilization cycles, or whether a hinge mechanism will degrade after repeated use. It can help teams compare design options, validate early assumptions, and make smarter trade-offs.
When embedded throughout the development cycle, performance testing serves as a continuous feedback mechanism. Rather than being reactive – waiting for problems to emerge post-launch – teams can be proactive, identifying potential weaknesses before they become costly recalls or field failures. More importantly, performance testing empowers teams to ask deeper design questions. How might users actually misuse the product? What happens if the instructions aren’t followed perfectly? These what-if scenarios, grounded in test data, often separate good products from truly great ones.
Learning from the Field: When Things Go Wrong
Despite best efforts, failures sometimes occur. Products are returned. Devices stop functioning. Customers report unexpected issues. In those moments, performance testing plays a critical investigative role. When a product repeatedly fails under certain conditions, patterns emerge. A cracked housing might point to a design weakness. A loose connection may reveal a vendor quality issue. Once the failure mode is identified, teams can isolate the cause and develop corrective actions that are not only fast, but effective.
This type of forensic testing is invaluable. It closes the loop between real-world experience and product development. It also provides evidence to support design changes, supplier shifts, or even updated usage instructions.
The Human Factor: Collaborating Across Teams
Effective performance testing doesn’t happen in a vacuum. It requires close collaboration between the design team, quality engineers, test specialists, and, critically, the people who understand how the device will actually be used. By working together early, teams can design test protocols that mimic realistic conditions rather than idealized ones. They can identify cross-functional failure points like those tricky areas where a minor software issue triggers a mechanical failure, or where an environmental factor causes sensor drift. These aren’t failures any one discipline can solve alone. They require integrated thinking, and performance testing becomes the common ground for that collaboration.
A Tool for Product Evolution, Not Just Validation
Performance testing isn’t just about checking off boxes for regulators. It’s a tool for continuous improvement, especially for products that evolve across generations. Often, new versions are based on existing platforms, and reviewing performance data from previous models can offer invaluable insight.
A team might look at the most common return reasons from a prior generation and test specifically for those risks in the new design. Perhaps a particular component failed frequently when dropped, or a seal degraded over time. Understanding those pain points early allows developers to stress-test their solutions before they reach customers. This proactive approach is even more important in today’s global, fast-changing manufacturing environment. Supply chains shift. Vendors change. Materials evolve. Even small adjustments can have ripple effects on performance, and testing helps teams stay ahead of those changes.
Performance Is the Promise You Make
When someone uses a medical device, whether it’s a patient, caregiver, or clinician, they’re placing trust in the product. That trust is based on a simple assumption: the device will work, every time, under the conditions it’s designed for. Performance testing is what ensures that promise is kept.
It’s not just a regulatory requirement. It’s a core part of delivering safe, effective, and user-centered healthcare products. And in a world where devices are increasingly personal, portable, and always connected, testing for performance is testing for trust.