Advanced Page Layout Example
Intertek is uniquely positioned with more than 20 years' experience to deliver end-to-end solutions that help organizations mitigate supply chain risk and protect their brand in both local and global markets.
Supply Chain Assurance solutions cover key areas of concern in the global supply chain management, social responsibility, quality, environment, and sustainability. Our global network of scientists, engineers, auditors, and regulatory specialists provide support to navigate complex scientific, regulatory, environmental, health, safety, and quality challenges throughout the supply chain.
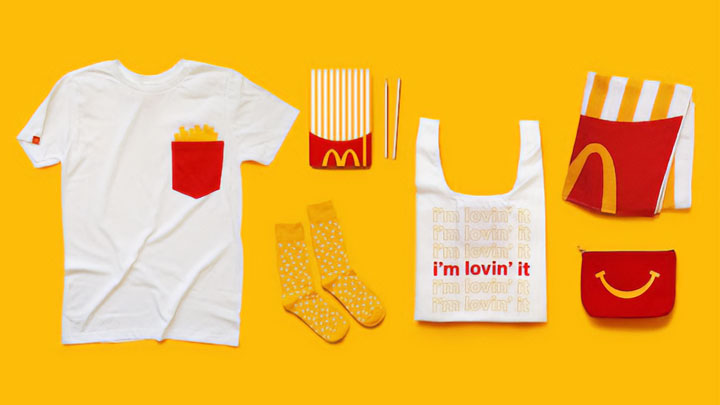
Our team can screen suppliers allowing you to move with confidence into production when changes are required.
Design Hazard Analysis® (DHA) is critical for ensuring consumer products have a design for safety. By integrating safety into the design itself and the modelling phases of product development, companies can effectively minimize production setbacks, costly rework, and post-distribution problems, such as failures and recalls. These resources include:
- Human Factors Assessment: Intertek's virtual and physical models accurately simulate the human anatomy. These safety criteria, specialized gauges, and digital simulations of the human airway effectively diagnose and demonstrate hazardous product characteristics by demonstrating exactly what will happen if a person comes into contact with a hazardous product. The models are anatomically correct representations of children and adults, developed from human anatomy studies, injury data analysis and human development research.
Assessing essential safety concerns and providing custom-made assessments to reduce product risk and potential hazards. Our safety assurance services support customers with:
- Risk and hazard assessment (both chemical substances and consumer products);
- exposure considerations;
- potential misuse of products;
- packaging compliance guidance and advice on mandatory label requirements; and
- product safety training.
Providing a pathway to decarbonization, helping bring sustainable products to market, and supporting end-to-end ESG needs. Our sustainability services include:
- Life Cycle Assessment (LCA)
- Ingredient Transparency & Health Declarations
- Responsible Sourcing
- Sustainable Claims Support
- Carbon Footprint & Water Footprint
- Corporate Sustainability Reporting
- GHG Emissions Support Services
- Sustainable Building Certification
- Management Systems Certification
Our global experts deliver timely and efficient services to screen, develop, evaluate and oversee the production quality of new suppliers around the world. When there is disruption within a supply chain, Intertek can provide on-the-ground support to assess production readiness or competency of potential vendors.
- Production Oversight – We are able to send experienced quality experts to your supplier to oversee production, and make sure that production quality has not been compromised.
- New Supplier Screening – Our team can screen suppliers allowing you to move with confidence into production when changes are required.
- Sub-Supplier Materials Assurance – When you are not sure of the source of your suppliers’ materials and components, Intertek will assess to ensure the product composition will meet your needs.
- Training – Our experts are capable of supporting quality practices for vendors in need of immediate support or that are dealing with quickly shifting employee base.
All McDonald’s suppliers and their facilities are required to adhere to the McDonald’s Supplier Code of Conduct (SCOC) and the Supplier Workplace Standard & Guidance Document (SWSGD) which can be found on @mcd - Supplier Workplace Accountability (SWA) Compliance. Intertek’s expert Outsourced Program Management team supports McDonald’s Supplier Workplace Accountability (SWA) Program through supplier onboarding orientation and supporting suppliers through the ongoing monitoring of compliance.
If you have any McDonald’s SWA related questions, please direct them to Keiko Millar or if you have any questions regarding Intertek’s Outsourced Program Management capabilities, please contact Kevin Fromme.
Our global network of regulatory experts helps our customers navigate their products through the vast range of regulations and standards around the world; we provide the confidence and assurance needed to minimize risk and efficiently bring packaging solutions to desired jurisdictions. Intertek has a range of assurance services to help you better understand both the market-driven and compliance requirements for packaging. Services include:
- regulatory consulting
- risk assessments
- extractable & leachables
- labeling requirements
- packaging design & design optimization
- environmental impact assessments
- extended producer responsibility and fee management
At Intertek, We provide expert regulatory support and analytical and chemical testing to help you meet global food contact regulatory compliance requirements to ensure the safe use of your products. Our Services Include:
- Food Contact Regulatory Compliance
- Global Food Contact Petitions and Notifications
- FCMs Analytical and Chemical Testing
- Sustainability for FCMs
- Good Manufacturing Practices (GMPs)
Intertek provides our customers with solutions to decrease the amount of packaging materials used, reduce the environmental impacts of their packaging and optimize packaging design to save costs throughout the supply chain, while ensuring the protection of the product is not compromised. Intertek’s sustainable packaging optimization services include:
Packaging Evaluation and Re-Design
- Product protection
- Legislative considerations
- Waste prevention, reusability, recyclability and disposal
Packaging Optimization
- Improve product protection and reduce defective products
- Reduce packaging and transportation costs
- Improve container efficiency and reduce environmental impacts
Green Packaging Claim Certification and Testing
- Independently verified claims
- Scope based on packaging environmental characteristics
- International Safe Transit Association (ISTA) packaging testing
- Intertek Packaging Solutions
- Total Quality Assurance - We understand the constraints growing companies experience with time, resources, and personnel. It’s why Intertek offers cost-effective and comprehensive operational solutions for all aspects of your business, from R&D to market compliance. We oversee quality processes, so you can focus on the growth of your business. Your brand is not only maintained – it’s protected!
- Quality Process Advice - We provide valuable insight into your product development process to minimize risk and increase speed to market. Our evaluation and recommended actions focus on policies, processes, best practices, and engaging the proper resources to increase transparency and reduce return rates.
All McDonald’s suppliers and their facilities are required to adhere to the McDonald’s Supplier Code of Conduct (SCOC) and the Supplier Workplace Standard & Guidance Document (SWSGD) which can be found on @mcd - Supplier Workplace Accountability (SWA) Compliance. Intertek’s expert Outsourced Program Management team supports McDonald’s Supplier Workplace Accountability (SWA) Program through supplier onboarding orientation and supporting suppliers through the ongoing monitoring of compliance.
If you have any McDonald’s SWA related questions, please direct them to Keiko Millar or if you have any questions regarding Intertek’s Outsourced Program Management capabilities, please contact Kevin Fromme.
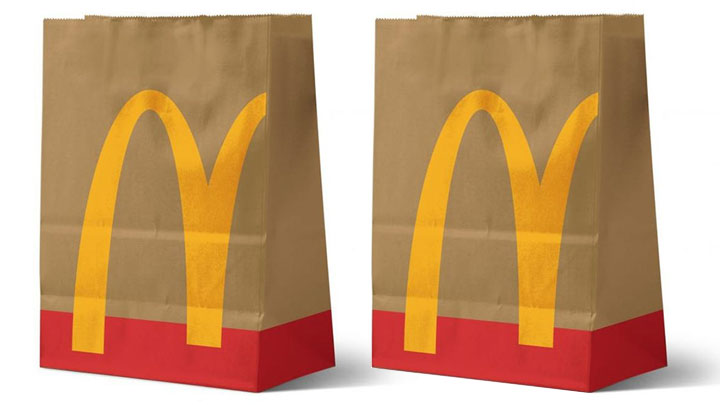
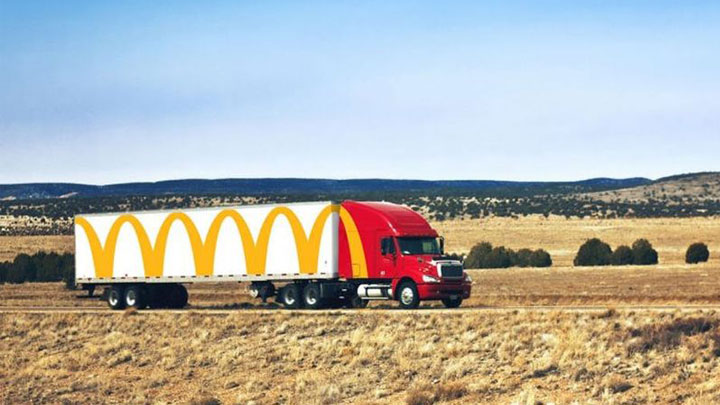
Intertek have delivered Supplier Quality Management System audits performed by GFSI qualified auditors since 2009. With its global footprint, Intertek can perform SQMS audits wherever your suppliers are located. For an efficient audit, we can conduct your annual GFSI audits with an SQMS addendum.
Intertek have provided Good Manufacturing Practise audits globally for several years. The (Unannounced) Good Manufacturing Practise audit is required for SQMS High Risk Category 1 Suppliers. These are suppliers in the raw or cooked meat and fish sectors, or who supply ready to eat salads or meals to McDonalds.
PQMS is a program designed for suppliers who manufacture packaging for McDonald´s. This program isn’t mandatory for suppliers who have a GFSI-recognized standard. This standard is designed for some regions only and does not apply globally.
Note: PQMS was a standard created by Arcos Dorados however from this year all packaging suppliers must be audited under GMP audit.
McDonald’s Distribution Quality Management Process (DQMP) audits focus on assurance that McDonald’s high standards of food safety and quality are maintained throughout the supply chain from manufacturer to restaurant delivery. From 2024 McDonald’s specific DQMP audits will be required in addition to GFSI requirements. Intertek can provide either stand-alone DQMP audits or an addendum to be conducted alongside your routine GFSI assessment.
Intertek is globally approved to perform Animal health and welfare, and Slaughter and Deboning audits for Cattle, Pig, or Poultry sectors. We can also offer the McDonald's Egg Laying farm audit in some countries.
Intertek has supported McDonald’s Supplier programs for several years. Intertek Wisetail & Intertek Alchemy supports every stage of an employee’s journey with an efficient, consistent, and tailored learning experience.
All McDonald’s suppliers and their facilities are required to adhere to the McDonald’s Supplier Code of Conduct (SCOC) and the Supplier Workplace Standard & Guidance Document (SWSGD) which can be found on @mcd - Supplier Workplace Accountability (SWA) Compliance. Intertek’s expert Outsourced Program Management team supports McDonald’s Supplier Workplace Accountability (SWA) Program through supplier onboarding orientation and supporting suppliers through the ongoing monitoring of compliance.
If you have any McDonald’s SWA related questions, please direct them to Keiko Millar or if you have any questions regarding Intertek’s Outsourced Program Management capabilities, please contact Kevin Fromme.
Intertek supports McDonald’s 3rd Party Food Safety Verification program by providing auditing expertise to assess the compliance of its restaurants with documented procedures. Our auditors assess risk across the whole restaurant management process, from supplier and ingredient controls to site maintenance, food preparation and waste management. In this way, Intertek supports the protection of the McDonald’s brand and its customers and improvements in food safety culture.
Intertek has supported McDonald’s 3rd Party Food Safety Verification program for several years. Intertek Wisetail & Intertek Alchemy supports every stage of an employee’s journey with an efficient, consistent, and tailored learning experience.
Our trained samplers take swabs to verify the efficacy of cleaning procedures, and samples of ingredients and finished products to ensure microbiological safety. Intertek’s ISO17025 accredited laboratories offer routine testing for indicator organisms and pathogens to demonstrate that controls in place in the restaurant are effective.
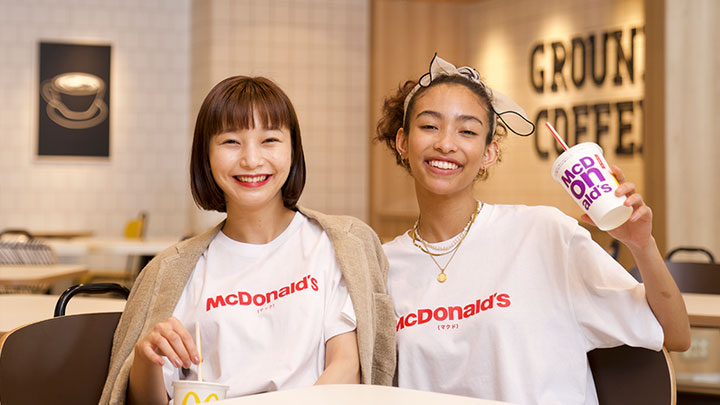